Our Engineering to your success
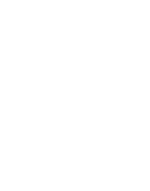
Engineering Services | In addition to Licencing or Technology Transfer of entire wind turbines, W2E offers comprehensive, detailed calculations, software, design, proofs and verification of individual components or systems.
On request, W2E will prepare studies on various drive train concepts, generator-converter systems or other auxiliary systems. Technical modifications of existing designs to adapt them to other site conditions (e.g. earthquake, typhoon, hot climate) are offered. The portfolio also includes load flow calculations and simulations of turbine behaviour in case of grid faults.
W2E also reviews third party designs and prepares reports and strength analyses or load calculations. Of course, in any case, strictly confidential.
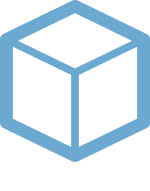
2D/3D CAD Design | W2E has 25 years of experience in the mechanical calculation and design of wind turbines in various drive train concepts and tower types:
- CAD 2D/3D design of the entire wind turbine (rotor, nacelle, tower and foundation) incl. the preparation of drawings and specifications
- Design of towers (tubular tower, lattice tower, concrete-steel hybrid tower and lattice-steel hybrid tower)
- Tailor-made designs and improvements for hot and cold climates, strong winds, earthquake and dusty regions
- Design of assembly and transport tools
- Design of lifting and repair tools

Load calculation, measurement and verification | Wind turbines are dimensioned by its structural behavior in combination with the highly dynamic loads caused by the environmental conditions. The interface loads of the wind turbine obtained by detailed dynamic simulations are the foundation of the wind turbine design. The load calculations are based on the DNVGL guideline and the IEC 61400-1 standard to fulfill the requirements of well-respected certifiers.
The dynamic load calculations are carried out using Alaska/Wind, MSC.Adams and FLEX5. Flex5 has been developed at the DTU Copenhagen and is permanently enhanced by W2E. In combination with the in-house postprocessing tool FLEXAnim W2E is able to provide a basic wind turbine design within a very short period of time. For advanced dynamic simulations W2E uses the general-purpose multibody programs Alaska from the TU Chemnitz and MSC.Adams from MSC.Software. MSC.Adams has been extended by NREL’s AeroDyn v14.0 for including aerodynamic loads. Both multibody programs are expanded by C++ and Fortran90 user interfaces for connection with the original controller software.
The load measurements on the wind turbine prototypes are carried out according to the IEC 61400-13 standard. The load calculations using Alaska/Wind, MSC.Adams and FLEX5 has been verified using real measurement data of a 2.0MW wind turbine prototype (more details). In addition, a multibody based Hardware-in-the-Loop test rig has been built-up to verify the original controller hardware.
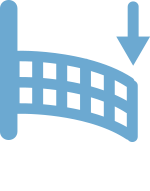
FEM and structural optimisation | W2E applies Finite Element Analysis (FEA) with regard to the applicable guidelines for the design and optimisation of all relevant structural components of wind turbines including castings, welded structures and composite materials.
To ensure realistic boundary conditions, the interaction of the analysed component with the surrounding structure is taken into account. With the software MSC.Marc, all kinds of non-linear effects, such as contact interfaces, material effects and clearance can be considered. Special attention is given to the modelling of bolted joints and bearings, taking into account the internal bearing design, contact angle, operating clearance, roller and raceway profiles, load distribution between rolling elements and temperature effects. Topology optimisation is a mathematical method that optimises the material layout within a given design space with the aim of minimising component masses. It is used at the concept level of a design process. W2E uses the TOSCA optimisation software to significantly reduce the masses of castings and welded constructions.

WTG control software design | The development of efficient control software is an essential part of wind turbine design. Due to the strong influence of the control software on the acting loads, W2E is constantly developing its software further. The 25 years of experience of the W2E experts pays off. In addition to the design of classic software, W2E works in parallel on the development of future-oriented, innovative control systems.
The classic controller schemes, which are based on PID algorithms and have been extended by advanced filter technologies, represent stable, robust modules. The advantages of this technology are the easy maintenance and the low demands on the controller hardware. All parameters used in the control software are the result of an optimisation process carried out for different operating points.
In order to be prepared for future developments, W2E cooperates with the renowned Institute of Automatic Control (read more) at the RWTH Aachen University to develop state-of-the-art model-based predictive control software (see details). The results of this research will be gradually introduced into the classical control software and tested in practice on W2E prototypes.
The application software is designed for different hardware platforms: M1 (Bachmann), WP4x00 (Mita-Teknik) and I/O field controller 750 (WAGO). The software architecture is based on standardised languages: Instruction list, function block diagram, sequential function diagram and structured text (IEC 61131). C and C++ codes are also used.
Supported SCADA systems are WPS (Bachmann) as well as MiScout and Gateway (Mita-Teknik). Interfaces to third-party SCADA systems are implemented according to IEC 61400-25 or other customer-defined protocols. Wind farm management applications are designed for different hardware platforms, e.g. M1 (Bachmann) and WP4x00 (Mita-Teknik) with interfaces to the energy supply company (utility) and direct marketing.
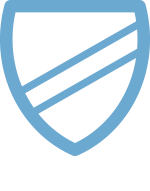
Safety System | The safety system is of great importance for the safe operation of the wind turbines. It acts as a personal protection and as a method against machine breakage. Hazard analysis and risk assessment are basic methods for the prevention of hazardous events which have to be performed according to the European Machinery Directive 2006/42/EC.
Safety functions are defined according to EN ISO 13849-1 and validated according to EN ISO 13849-2. Their Performance Levels are calculated and verified. Sensors, logic unit and actuators for avoiding the most serious hazards (overspeed and exceeding of vibration limits) are implemented and verified according to Performance Level d. Further safety functions concern cable twisting in the so-called loop, short-circuit, emergency stop, transformer protection and failure of the control system. W2E uses safety switchgear devices from Pilz, Bachmann, SIEMENS and Mita-Teknik. W2E offers comprehensive solutions for wind turbine protection by fire detection and (optionally applicable) automatic fire extinguishing equipment as well as fire prevention measures such as residual current monitoring, earth fault detection, arc flash detection and correctly designed TN-S or IT network structures.

Experimental investigations of noise and vibration | Using its own measurement equipment W2E is active in the field of experimental structural dynamics. The following investigations can be carried out:
- Application of classical and operational modal analysis to all wind turbine structures (nacelle, tower, blade) for a modal parameter identification
- Analysis of tonalities and its reduction
- Sound path analysis
- Application of vibration absorbers
- Procedure design for sound reduced operation
- Optimisation of wind turbine control for vibration reduction.
The staff of W2E has large experiences in structural dynamics of large mechanical structures, such as wind turbines, vessel and offshore structures. The structures can be investigated with respect to its modal and forced vibration behaviour. As a result of these investigations the structure can be optimised with respect to its structural behaviour or wind turbine control optimisation. Closely related to the vibrational behaviour the noise of wind turbine structures can be investigated. As a result of these investigations the tonalities of a wind turbine can be reduced. Due to the design and operation of wind turbines W2E has large experiences in the procedure design for sound reduced operation.
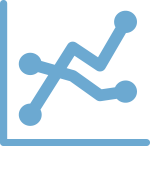
Modelling and simulation of electrical characteristics | The desired grid behaviour plays a key role in the overall system design. The increasing share of installed wind turbines requires excellent electrical properties in order to achieve a stable and highly available grid. The complete drive train, the pitch system, the converter (DFIG or full-size converter with PMG) and the wind field are modelled. The control algorithms of the sub-models are 100% identical to those installed in the wind turbine. The characteristics of the wind turbine on the grid are simulated using the PowerFactory software (DIGSILENT company). Furthermore, load flow calculations and dynamic simulations of individual wind turbines as well as entire wind farms are carried out (steady-state current, voltage, power, power factor). Different grid error states are analysed (3-pole short circuit, 2-pole short circuit, LVRT, HVRT).
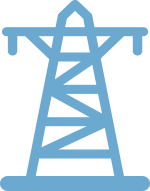
Electrical Engineering | The generation, conversion and distribution of electrical energy as well as the electrical auxiliary and control devices are indispensable components of modern multi-megawatt wind turbines. The electrical design is based on the DNVGL guideline as well as the European standard and IEC norms to realise reliable and highly available functions of all electrical systems.
W2E offers comprehensive services in the field of electrical design. Detailed specifications for generator, transformer, pitch system, azimuth system, control cabinet including schematics, converters, tower equipment and cables are prepared according to the specific customer needs (environmental conditions, local requirements, local content). W2E works closely with first-class, internationally established suppliers and qualifies new local suppliers where necessary.
W2E considers different types of interfaces between neighbouring systems and components. Different fieldbuses are configured: Profibus, CANopen, Profinet, Modbus, Ethernet, etc. The calculation, specification and laying of cables results in the cable list, cable routing drawing and definition of cable sets including their plug-connectors.
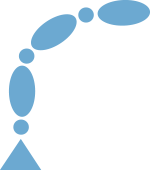
Multi-body simulation | Multibody simulation is the most powerful dynamic simulation tool for complete mechatronic systems. General purpose multibody simulation tools, such as MSC.Adams and Alaska, provide the possibility to calculate any arbitrary dynamic system.
Multibody systems are a simulation method for complete dynamic systems with a practically unlimited depth of details. Typically, multibody systems comprise a finite number of rigid and flexible bodies connected via ideal constraints and joints. Furthermore force, damper and actuator elements can be included into system simulation. The flexible bodies are typically modelled by a modal representation allowing the simulation of large rigid body motions covered by small displacements keeping the degrees of freedom at a minimum level.
The extension of multibody systems by user routines allows the consideration of automation and control routines. Furthermore, there exist predefined interfaces to MATLAB/Simulink for designing and testing control algorithms using a realistic control path.
The W2E staff has strong experiences in multibody simulation in the fields of wind energy, aircraft engineering and general research on that topic. A close cooperation in research and education to the Chair of Technical Dynamics (see more) of the University of Rostock keeps W2E up to date on recent developments in multibody technology.